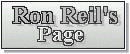
How to Make Twisted Copper Wire Bracelets
This
is a picture of two twisted copper wire bracelets I recently made
for Christmas gifts. These are not intended to be used as jewelry, but
for arthritis pain relief. These can easily be made by anyone with a
reasonably equipped home shop. They are made from heavy gage copper
grounding wire, available at Home Depot. I use mostly 4 gage wire, but
some people prefer a lighter gage bracelet, so you may want to get some
8 gage also. The heaviest gage at the Boise Home Depot is 4 gage. Each
bracelet requires 16" to 18" for an average wrist, and 20" or more for
someone
with big wrists. A person with small wrists may need only 14", or even
less. The top bracelet in the image has 20" of wire in it and the one
below it 18".
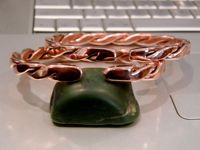
Cut
off an 15" to 20" length of copper wire, depending on the size of wrist it will be for, and gently straighten it as
much as possible with just your bare hands to prevent marking it. Then, using a chisel, notch
it 1/3rd through in the middle of the wire, fold it in half with the
notch inside the fold, and using a polished wide faced hammer, such as
a jeweler's hammer, gently work it until it is totally folded flat with
no space between the two wires, and no bends or bumps. I use a
cobbler's hammer I obtained at the flea market for which I made a
jeweler's hammer handle. The very wide flat face on the cobbler's
hammer, and the curved edges I put on it will not mark the copper, and
it makes a very fine jeweler's hammer. Expect to invest a half day
dressing the face of the hammer to make it mirror smooth, and give it
smoothly rounded edges so it will not die mark your copper wire, or
other soft metals.
You need to work on a totally smooth faced
anvil. If you do not have one, get yourself a big chunk of scrap steel
and put a polished face on it to use as your anvil. Copper is so soft
it die marks if there is even dust on the anvil, so both the hammer
face and the anvil need to be very smooth. Below is a picture of the
anvil I reserve strictly for non ferrous metal work, copper, silver,
and rarely gold. The top is glass smooth and does not put even the
smallest die mark into the soft metal. This is an image of what it
looked like right after I brought it home and seated it on sheet lead
so it would not make the acorn table ring, or allow the anvil to ring.
That hammer came with it too, both were a gift to me. If you can find a
farrier's anvil like this, reserve it for this kind of work. It has a
unique feature that makes it of great value when working items like
bracelets. The top of the horn is not round like the horn on a
blacksmith's anvil, but flat, so you can use the top to take curvature
or bend out of the
metal while you are fining a shape, and bracelets need to be perfectly
shaped, so that flat top is a wonderful feature. Most smiths do not
like the flat topped horns on farrier's anvils for regular iron
smithing, so these anvils really are perfect for jewelry work. The flat
is of course to allow the farrier to take some of the bend out of horseshoes to open them out.
Once
you have the wires completely parallel and tight against one another,
hold the non folded end tightly together and put about a half inch into
a vise and secure it, with the wires sticking straight up. Use a
Crescent wrench, or better, a twisting wrench made from an old Ford
wrench, and clamp the wrench on the top 1/2" where the shallow
notch and fold are. Twist it to the point that it will not twist any
further without starting to deform and bend the twisted shaft out of
line. Here is one of my smaller twisting wrenches that I made from a
Ford wrench.
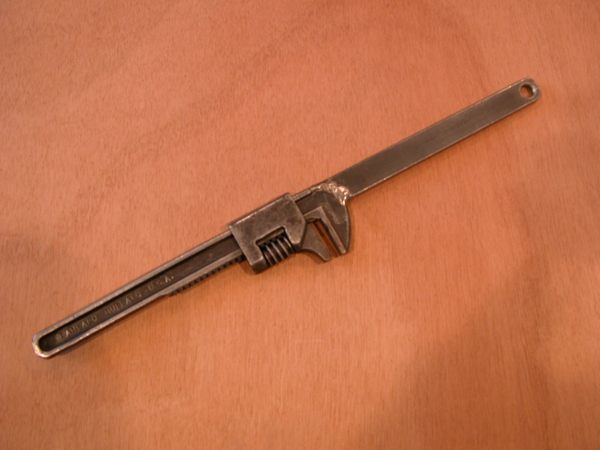
Remove
the twisted pair of wires, and using the jeweler's hammer, gently
straighten it and make sure the two ends are still in the same plane,
and with no space showing between them. Gently clamp it in the vise and
twist or untwist it until the ends are in the same plane if necessary.
I use a 4" post vise with smooth copper jaw covers for jewelry work so
as not to die mark the copper or silver. The post vise also allows me
to hammer on the work if I need to, and the force of the hammering is
transferred to the concrete floor instead of the vise and the bench.
This vise, like the farrier's anvil, is used strictly for non ferrous
metal work. It is mounted on my foundry bench, which is steel topped,
and also serves as my jewelry bench.
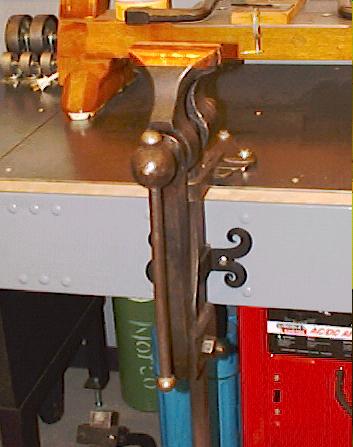
Now,
clamp the wires in the smooth vise jaws with about 2" sticking out to
the side, and cut a short piece of small diameter, say 12 gage, pure
copper wire and lay it on top and between the two parallel and non
twisted portions of the wires right at the end. This little piece of
copper is used as filler rod. Then use your oxygen-acetylene torch,
best to use a Henrod 2000/Cobra torch, because of its laminar flow
characteristics and very low operating pressure, to flow the thin piece
of copper wire into the space between the wires. Once that side is
completed, turn it over and repeat the process on the opposite side.
Then do it all again on the opposite end. You don't need to make it
smooth or pretty, just make it solid, and with 100% penetration of the
metal so there will be no openings in the end of your bracelet when it
is done. You will file and trim them to create those nicely shaped ends
you see in the picture at the top of this page.
A word about
flowing/welding the copper.... Copper has ultra-high heat conductivity,
exceeded only by silver, so it may take you a few tries to successfully
flow the copper together without having the entire end melt and drop on
the floor. It is a delicate process of moving the tiny flame back and
forth to heat the spot you want to melt just enough to flow it
together, but not so much that it loses all its strength, becomes
liquid, and drops off. You want a very tiny flame with a blue cone
about 1/4" long, and about the diameter of a pencil lead. If you can
hear the flame you have too much pressure and it will blow the copper
away, or melt it and drop the entire end of the bracelet to the floor.
Keep your feet out of the way when flowing/welding copper.
Once
you have the two ends welded into a solid piece of copper, you can then
relax because the rest of the project just takes time, but it is fairly easy. If the welds
are gobby, with big drips, file them off and clean the ends up
carefully. You do not want to mark the twisted copper wires with the
file in the process. Here is where file control becomes very important.
Just remove the worst of the excess copper. You will use your jeweler's
hammer to work it down into the tapered shape you want to end up with.
It may taper on the sides or not. Look at the top picture. The top
bracelet does taper and the lower one hardly at all. You do want it to
taper top and bottom however, as that will make it more comfortable to
wear.
As you hammer, try to keep the two ends in the same plane.
The twisted copper will make them rotate slowly, so clamp an end in the
vise occasionally and retwist, or untwist, just enough to keep them in
the same alignment as you work.
Once you have the ends roughed
out, lay the piece on your anvil, with the flats of the two ends
parallel to the face of the anvil, and gently and carefully hammer the
full length of the piece to form equal sized flats on both sides of the
piece.
I have also cleaned the piece shown in the image with a fine steel wire
wheel. You will need to keep reversing it top for bottom to flatten it
equally on both sides because the metal in the side against the anvil
will not move as much as the hammered side. This is where the quality
of the dressing on the face of your hammer will really make a
difference.
If the edges of the hammer face are not curved away from the face
enough you will die mark
the copper with the edges. I strongly urge you to pick up an old
cobbler's hammer at a flea market and make a jeweler's hammer from it.
They are cheap, about $3 to $6 at the time of this writing, and they
are really useful for making several different types of fine, light,
hammers.
As
you work the copper it work-hardens. You may use the torch, or the
forge, to anneal it and make it soft again, but I never do. I like it
to harden and become spring copper, and as it does so it becomes much more
difficult to work. The advantage to the hard copper is it retains its shape in the rough
environment it is subjected to on a man's wrist. For a woman, feel free
to anneal it. Annealing coper, or silver, requires the exact
opposite technique used for steel. Heat the copper to a red heat and
quench it. If you quench it in a "Pickle" solution, available at any
jewelry supply store, and most rock shops, it will come out of the
quench very bright and clean. I don't bother with using the "Pickle"
for copper because it gets throughly cleaned when I do the final
finishing.
Back to the anvil...flatten the top and bottom
equally, and enough to be pleasing to the eye. Also flatten the sides
to a lessor degree, and work back and forth between all the faces until
you have no forging distortion on the flats. Also, at this time you need to use
fine jeweler's files to put the final shape on the two ends. Do it now
because it is much more difficult to work on them once it has been
formed into the oval bracelet shape.
Probably the second most
frustrating part of the entire process is now at hand, forming the oval
shape in the bracelet. The first time you do it you will think it is
impossible to get it properly shaped. The copper is forgiving, so you
can unbend parts of it on the flat of the horn and rebend it as many
times as necessary to perfect the shape. It is all done with the
jeweler's hammer while working on the outermost 3" of the horn. I like
to close my bracelets to within 3/8" to 1/2" for a man, and an inch for
a woman. Women remove theirs, men don't. I always offer to fit a new
bracelet to its owner if it is a man due to how difficult it is to open enough to get
it over their wrist. Also, I generally need to reshape it to more closely match their
wrist to make it as comfortable to wear as possible.
Once
you have it shaped to your satisfaction, clamp it in the vise, and
using a half round fine jeweler's file, take the sharp edges off the
interior hammered flats all the way around the interior circumference.
If you don't, it will be very irritating on a man's wrist when he is
working with tools. If they are made right, the owner will not even
notice he has it on most of the time. The copper bracelet on my right wrist has
been there for the last 3 years without ever having been removed, and
the one before it was there for about 10 years. The only reason I
replaced the first one was due to my "new" twisted design that I like
better. I have another twisted one that I wear on the upper part of my
left arm, just about an inch below the elbow. They are not nearly so
easy to get used to, and require a long "break-in" period for your
muscle to form a permanent groove in it all the way around your arm,
into which the bracelet seats and will not move from. They are nice
because they are out of the way and hidden when wearing a long sleeved
shirt, but some people find them uncomfortable, especially during the
first month or two.
The last step is the polishing. Probably you
will not bother with dental lathes like I use, but if you see one at a
flea market, absolutely do not let it get by you. They are
wonderful multi-speed tools, and ultra precision. These old dental
lathes are much higher quality than the best new jeweler's
lathes/buffers. Below is a picture of my dental lathe, on the right, and
a home made buffer on the left. Use high speed motors to make your
buffers. That wire wheel on the far right has hair-soft steel wires in
it, which is what you will need to use to put your initial finish on
your bracelet, or even the final finish perhaps. It produces a matt
finish. The hard felt wheel on the left side of the dental lathe is
used with jeweler's rouge to polish the metal, and to remove any
die marks. It actively cuts the metal away but leaves a high polish at
the same time. Use larger diameter hard felt wheels for more rapid
cutting. I use the large diameter cloth buffer that you see mounted on the home made buffer
motor to put the final finish on the metal. Use rouge with it too,
either red or green, depending on the degree of polish you want, but do
not mix them on one buffer. Dedicate each buffing wheel to a particular
rouge, and use it only for that. I mostly use red rouge. You can put
absolutely mirror finishes on metal with these tools.
The dental lathe
is dual speed. Move the switch left and it is on slow, to the right,
high speed. Dental lathes are so well made they are almost totally
silent when they run. BTW, the wire wheel on the counter on the right
is a brass wire wheel for applying fine brass highlights to hot iron.
It also has hair-soft wires. I run it on slow speed when applying brass
highlights to hot metal, and it has an almost airbrush effect.
One
caution regarding your buffing wheels, when you are not using them,
keep them wrapped in plastic so no contaminating shop dust gets on
them. The dust may contain silica, or metal dust from grinding, and the
dust will be much coarser and more abrasive than the rouge, ruining the
quality of your finish, and ruining the buffing wheel.
Page By: Ron Reil
©Golden Age Forge
24 Dec 07